In the 1970s, Toyota system was the first to introduce kaizen. The focus was on projects related to improvements, with the approach that involved participation of a cross-cultural team. The aim was to improve the working area by achieving certain targets. Thereafter, the word kaizen stemmed from the 'change' and 'continuous improvement.' The purpose of kaizen methodology is to control the working environment operations, as well as workers and processes' efficiency improvement. It can be implemented by any organization and serve as the key tool that would help the business remain competitive.
Kaizen has been used as an effective instrument that helped to change the work experience, work proceedings, and work culture. It is treated as one of lean tools that assist in running the operations smarter by removing unneeded waste, which does not bring any value for the potential customers. Moreover, with kaizen practices implementation, the mind set of employees fully changes, and they see the possibilities of improvement everywhere, with the thought that it would be beneficial for them at the first place (Hashim, Zubir, Conding & Jaya 2012).
The purpose of the following paper is to look more precisely at the practice of kaizen. It gives proof on how it can be beneficial for companies and employees within them. Examples of organizations, which have successfully used kaizen practices, are provided. Additionally, the deeper understanding of the importance of kaizen methodology is argued. Moreover, the paper will review Six Sigma tools that can help a company to gain continuous improvement.
Why Kaizen
Today, numerous companies try to build their business by using the best world practices and kaizen methodology has proven to be the most successful instrument that is used to increase efficiency, receive high results, and motivate people. This philosophy of continuous improvement is the driver and a starting point of all initiatives related to lean. The event of kaizen gives numerous firms an opportunity to make certain focused workplace changes, but they need to be carefully planned and smartly implemented. If the business takes a path of kaizen philosophy, it should help it to establish long-term benefits related to efficiency improvement that would assist a company in remaining sustainable and competitive on the market. The main reason why the majority of improvement efforts fail is the inability of the enterprise to reap the cultural and financial rewards because of the lack of execution, planning and reliability in the organization (Ortis 2006).
Short History Overview
Massaki Imai coined the term 'kaizen' in his book in the 1980s. Since then, it has been mostly used in association with Japanese companies' performance management. In addition, it is acknowledged as a key factor that helps them to remain at the leading position among their world competitors during the last three decades. Some mention that such success is due to the involvement of the staff into all improvements related to the philosophy while others say that high results are achieved because of proper implementation of tools and techniques related to waste cutting. Other group of researches claims that kaizen is just an approximation to already established approaches of the management, such as Toyota Production System and Lean Manufacturing. Such working environment requires the top and middle managers to look into methods and projects that would help to increase customers' satisfaction, reduce costs, improve quality measures and process innovations more effectively. Massaki Imai has provided his own definition of kaizen, according to which this business strategy is about involving every employee of the organization to work for one task that is related to operations' improvement without large capital investments.
If to look deeply into scholarly sources that investigate the phenomenon of kaizen, many inconsistencies and controversies may be observed. The Japan Human Relations Association (1990) has stated that kaizen comprises of problems that employees face on a daily basis. It is important how they solve those issues. From the ethical point of view, kaizen can be understood as internal force of each worker that is used by him or her in order to address daily problems and get satisfaction because of the value of his/her work (Su?rez-Barraza, Ramis-Pujol & Kerbache 2012).
The on-going set of improvement involves both workers and managers that are constant. The negative consequences of the Second World War forced the Japanese companies to look into smarter solutions to revive the economy. The problem must be recognized at first, while the need of its solution would be established immediately. Kaizen is about establishment of problem-awareness as well as problem solving that would follow the identification stage. The reached level of the improvement has to be standardized and fixed to proceed with the movement further. The heart of kaizen approach is the balance between continuous improvements of routine and ideas for future constant improvements.
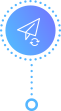
STEP 2
Make the Payment
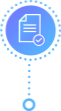
STEP 4
Download Your Paper
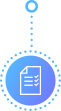
STEP 1
Place an Order
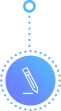
STEP 3
Communicate with the Writer
Importance of People
People are the key asset of kaizen management. This philosophy needs a development of a certain firm-specific human capital though job rotation, on-the-job and cross-functional training. The commitment of all company staff is very important as front-line workers are the ones to recognize and target the problem by working in teams and trying to identify the possible similar improvements in other areas. Individuals who are at the lower level are the most effected by a change so they must be empowered most of everyone. Moreover, the structure of the organization must be transparent and based on no-blame culture. In this way, workers will make conclusions and suggestions based only on data provided but not on the personal opinions of top managers or their own ones. The main objective is to sustain the achieved level that was gained due to waste removal and further improvement. However, the culture of the organization is not the frame that can capture the success of kaizen implementation since organizational practices and characteristics are far more important. The success of kaizen initiative is based on commitment, discipline, empowerment, and pragmatism cultivation (Magnier-Watanabe 2011). In order to ensure successful kaizen program implementation, a champion must be nominated, whose efforts would be fully put into that. Preferably, the person who is to occupy this position should not come from middle of top levels of management but from some supervisor's positions, with the good knowledge about project management (Ortis 2006).
Kaizen as an Incremental Change
Changes are not that easy to accept for everyone. Innovations can be radical and incremental. The features of kaizen are quite clear once they are used in comparison with radical innovation, but it belongs to the type of incremental innovation. Human resources use conventional know-how and collective and incremental team efforts in order to use kaizen practices within the organization. While everyone in the hierarchical level of the organization is involved in implementation of incremental changes, a stable trust ground must be built among the employees. The horizontal organization structure is the perfect fit for kaizen. It should come with an opportunistic knowledge acquisition (Magnier-Watanabe 2011).
Methodology in Practice: Japan
This is now obvious that kaizen is about how people manage their problems, but this methodology may be easily explained based on particular examples taken from companies that operate in the Japanese society. The steel industry of Japan has always been the source of innovations and money for the governmental treasury. The incremental improvements were crucial for this industry as without them the iron and steel businesses would fail to introduce new technologies successfully. Nippon Steel Company (NSC), which is an integrated steel manufacturer, was the biggest producer of steel since ages, was a pioneer in kaizen techniques implementation. Kaizen and "zero defects" activities have been started to be implemented in this company since 1962. Certain voluntary activities were practiced, and the management of the company has faced an issue regarding the equal workload between teams because many tensions arose. Nevertheless, more and more people were participating in the activities related to achieving the "zero defects" and eventually helped the company to decrease stoppages in production lines and improve efficiency and quality. Safety, TMP, and quality were nominated as the key aspects of kaizen as individual mandatory activities. The specific goals were to be achieved with the help of number of projects that are done during the working hours of the employees. Everything was recorded in NSC by means of storyboards, system records, and on-line recording of the existing progress. This circumstance gave the managers a possibility to monitor the progress of the system and specialists' training or specialists were assigned based on each particular case. All kaizen activities revolve around the work team structure, where autonomous units are created to take the responsibility for challenging tasks and police deployment processes. With time, participation in kaizen became a routine that can assist people and a business to be effective. Activities, which are related to kaizen, are not extra paid, while some companies might provide some bonuses. In any case, recognition and acknowledgement of contributions is valued higher than money (Brunet & New 2003).
Methodology in Practice: The USA, Malaysia, and Thailand
Another example of kaizen methodology implementation might be a case of New United Motor Manufacturing, Inc. (NUMMI), which was established in 1984 in California. It is a venture of Toyota Motor Corporation and General Motors Corporation developed as an experiment by combining American standards and 'lean practices' of Japan. The newly created company has started to hire employees and train them according to the expected standards. Some of the newcomers were enabled with an opportunity to go to training in Japan. The firm has signed off a trade union agreement with the United Auto Workers Union that stated the inability of NUMMI to lay off employees under normal economic conditions. Nonetheless, even during the times of recession, the number of workers was not increased due to kaizen projects that brought a lot of economy for the operating plants. The business was further selected as an example of the best labour-management cooperation within the US. Thereafter, the case of NUMMI demonstrates how kaizen can be successfully practiced through collective membership and horizontal structure (Magnier-Watanabe 2011).
The automotive sector of Malaysia is one more example of how kaizen can help the business. National Automotive Policy (NAP) was introduced by the specialized organization in order to improve safety, quality, and production standards of the automotive sector in Malaysia. The demands were quite high and challenging at the same time, the main objective of which was to exceed the expectations of the customers. Thus, kaizen was chosen as the best practice, and automotive industries needed to start with the organizational learning promotion. Kaizen practices are leading to continuous improvement (CI) through innovations and sustainability, associated with individual performance and company's efficiency. People were entitled with an option of making their own decisions and had enough freedom to implement changes. The only condition was that everything needed to be in a frame of kaizen practices. Kaizen has significantly helped the automotive industry in Malaysia, and even the studies related to its results have been taken as a benchmark for other companies within the country (Hashim et al. 2012).
The other factory that is geographically located in Thailand and is a subsidiary of Japanese manufacturer of computer products has been also 'targeted' by kaizen activities in order to reduce their costs. Company had three expatriates, while the rest of the employees were Thai, who occupied the managerial positions. The top managers introduced the kaizen activities directly to line operators, with the emphasis not on 'cost cuts' but on 'enjoyment of kaizen activities.' With time, this activity has started to be perceived as fun by workers, and they were fully engaged with kaizen. As a result, the productivity number has increased by 15% due to successful practice implementation from the Japanese management style (Oki 2012).
Six Sigma and Kaizen
As it has been mentioned in the beginning of the paper, it is important to state how Six Sigma as an instrument of kaizen can help to make breakthrough improvements. Six Sigma methodologies include DMAIC projects and other. Thus, the cost savings are not always seen in the bottom line and the main reason to that is the absence of maintenance and minor improvements. In addition, the systematic improvement, monitoring and further usage of kaizen activities is very important as the process might degrade. See screenshot 1.
On the contrary, the organization would get into a better financial position once it follows the established processes and the management of the organization is looking into further constant improvements. It is so, because the process of improvement becomes regular and forces further benefits. See screenshot 2.
It should be reviewed how it can help the specific company that is four-wheeler manufacturer the title of which would remain unknown. The Black belt projects has been done in one of the lines as a part of Six Sigma methodology and was related to the completely built units (CBU) of automobiles in terms of the sampling inspection cycle time. At the beginning of the project the sampling inspection cycle time was three working days or 24 hours.
When the project was almost finished and the results have been monitored through the Control Phase, the time that was needed for the operation was drastically cut to one working day or 7.7 hours. The cycle time has been reduced by two-thirds. The selected employees have been assigned as the owners of the belt project. In addition to that, other workers have been further looking into kaizen activities, which helped not only to get the further better results but also to improve the motivation of the employees.
The belt project had an action that was related to the sampling process, which was about taking measurements of the turning radius of the vehicle. Before the project, the operation required two workers and 20 minutes. After the kaizen event, the idea about putting a pipe that would simplify the process came out and the time was reduced to 5 minutes and with only one worker involved (Choudhury). The following examples prove how Six Sigma and kaizen can help the organization to reduce costs, improve and engage more workers, so the motivation would be increased.
Usage of Other Tools
"Failure Modes and Effects Analysis" (FMEA) is another part of the Six Sigma methodology and is about techniques that are targeting the future issue and eliminate the risks that are related to project process and can hinder the implementation process. It is about further detection and elimination of the potential defects that can deteriorate the quality of the product (Six Sigma Online 2015).
Another valuable instrument of Six Sigma is Poka Yoke, which is a Japanese term and is also known as Mistakes Proofing. It is aiming the waste reduction in such categories as time, resources and energy. It is trying to involve the employees so they would be encouraged to look for the mistakes, so the suggestions would come out of the employees and the mistake would not occur again (Six Sigma Online 2015).
Less Successful Examples
The researches that reveal why kaizen activities did not bring the expected results also include important information that helps to see what was wrongly implemented within the organizational structure. One of such case studies of a large equipment manufacturer was taken as an example. It has started to practice kaizen since the 1980s on both manufacturing and non-manufacturing working areas with the ratio 70/30 accordingly. Thereafter, the enterprise was considered to be mature in terms of innovations and continuous improvement, but particular events caused variations in outcomes. The event that was initially intended to improve the raw materials quality has been assigned a status of 'non-implemented.' By putting its efforts, the team did job well and the objectives were reached, but the targets were not specified. There were another 12 cases like the aforementioned one, certifying that an objective was successfully achieved on a technical level. The main reason why this aim was not achieved was because the goals were not communicated by the team clearly, the lack of key function representation by the team, and the presence of decision-making authority in this case was limited. Support by the management team during this process was not seen, which broke the communication (Farris, Aken, Doolen, & Worley 2008). This case provides a clear example on how the kaizen activities might not be implemented due to the presence of some 'gaps' in the organizational structure of the company.
Kaizen practice affects the working area, but it has much influence at social, cultural and technical system of the enterprise, which has impact on the aforementioned working area. Kaizen works like a tool that helps to emphasize that (a) stewardship impacts learning that is aimed at helping employees to get the feeling of being valuable; (b) to share the responsibilities; (c) freely share information (stop the line if safety or quality is jeopardized) and (d) see oneself as a 'link of a bigger chain' that has a direct influence on the company's efficiency and customers' satisfaction.
The culture of continuous improvement may be created by combination of two important things, involving work area, processes and products, with the successful implantation of proper human resources practices. Innovation is the most important part of business growth and long-term strategy development. It is an integral part of production as it covers product, process, and technical types of innovation. Thereafter, kaizen helps to support the vital 'function' of business by changing mind set of people, who try to implement the lean practices in order to achieve continuous improvement and do it as a part of everyday job activities.
The paper has provided as specific example of using Six Sigma methodologies and kaizen activities, which can help multiple organization on the path of continuous improvement. The paper also has shown that many companies, which have implemented kaizen, have managed to improve their safety, quality, financial and managerial operations. Some organizations failed owing to such factors as work environment and organizational culture. Kaizen is about making changes without large investment. It is about monitoring results and changing the company's culture and improving the high-cross functional cooperation.